Working at Heights: Tips and Info on Scissor Lifts
Want to learn how to use scissor lifts safe and well? Read more for tips on types, rules, and tricks to work high up with no risk. This guide will help you pick and use the best lift for your job with ease.
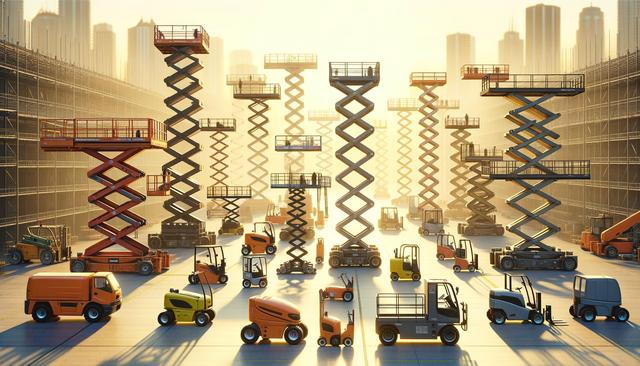
Understanding Scissor Lifts and How They Work
Scissor lifts are a type of mobile elevated work platform (MEWP) designed to lift workers and tools to various heights safely and efficiently. They operate using a crisscrossing metal support — the “scissor” mechanism — that expands and contracts vertically. These machines are often used in construction, maintenance, and warehouse operations where vertical reach is necessary but space is limited.
There are two broad categories of scissor lifts based on their power sources: electric and engine-powered. Electric scissor lifts are commonly used indoors due to their quiet operation and zero emissions. In contrast, engine-powered models, which run on diesel or gas, are more suitable for outdoor use, especially on uneven terrain. Understanding the differences can help you choose a lift that matches your project’s environment and safety requirements.
Key components of a scissor lift include:
- The platform – where workers stand and store tools
- Guardrails – for fall protection
- The base – containing the power unit and wheels
- The scissor arms – which raise and lower the platform
Before using any scissor lift, it’s essential to review the manufacturer’s manual and ensure all safety features are functional. Familiarity with its controls and safety systems will help prevent accidents and improve job efficiency.
Different Types of Scissor Lifts
Scissor lifts come in various models that serve different tasks. Choosing the right one depends on your specific needs, such as height, weight capacity, and work environment. Here are some common types:
- Hydraulic scissor lifts – Use hydraulic oil to raise and lower the platform. These are straightforward and reliable but may operate slower in cold conditions.
- Electric scissor lifts – Ideal for indoor use, these lifts are quiet and emission-free, making them suitable for warehouses, retail, and event setups.
- Diesel scissor lifts – Designed for rugged outdoor work, these have higher weight capacities and can handle rough terrain.
- Pneumatic scissor lifts – Powered by air pressure, these are environmentally friendly and good for settings where avoiding pollutants is critical.
Each lift type offers specific advantages, so evaluating your job’s location, required lift height, and operational needs is crucial. For example, if you’re working indoors with limited ventilation, an electric model would be more appropriate than a diesel-powered one.
Safety Tips for Operating Scissor Lifts
Safety is a top priority when using scissor lifts. Although they are built to be stable, accidents can occur due to misuse, poor maintenance, or environmental hazards. Following established safety guidelines can significantly reduce risk and ensure smooth operations.
Here are some essential safety tips to keep in mind:
- Always perform a pre-operation inspection. Check brakes, guardrails, tires, and emergency controls.
- Use personal protective equipment (PPE), including a hard hat, harness, and non-slip footwear.
- Never exceed the lift’s weight limit. This includes the operator, tools, and materials.
- Avoid using the lift in high winds or extreme weather conditions.
- Only operate the lift on stable, level ground. Use outriggers if available.
Operators should also be properly trained and certified. Training should include both theory and hands-on practice, covering how to use controls, understand load limits, and respond to emergencies. Regular refresher courses help maintain awareness and adapt to any changes in safety regulations.
Maintenance and Inspection Essentials
Regular maintenance and inspection are crucial for keeping scissor lifts in safe working condition. Over time, wear and tear can affect the performance of hydraulic systems, electrical components, and mechanical parts. Ignoring these issues can lead to breakdowns or accidents, especially during high-stress tasks.
Maintenance plans should include:
- Daily checks – Look for leaks, tire damage, and loose parts before each shift.
- Weekly inspections – Test the lift’s performance and examine hydraulic fluid levels.
- Monthly reviews – Inspect battery health (for electric lifts), engine components (for diesel lifts), and lubrication of moving parts.
- Annual servicing – A comprehensive inspection by a certified technician to ensure compliance with safety standards.
Keeping a maintenance log helps track repairs and monitor recurring issues. It also serves as proof of compliance for workplace safety audits. Using original equipment manufacturer (OEM) parts during repairs can extend the lifespan of your lift and maintain its safety integrity.
Choosing the Right Lift for the Job
Selecting the right scissor lift involves evaluating several factors, such as job height, platform space, terrain, and work duration. A mismatch can lead to inefficiency or even pose safety risks, so understanding your project requirements is key.
Here are some questions to consider when choosing a lift:
- How high do you need to reach?
- Will the work be indoors, outdoors, or both?
- Is the terrain level or uneven?
- What is the total weight of workers and tools that will be on the platform?
- Do you need mobility around the site?
If your job involves frequent repositioning or working in tight indoor spaces, a compact electric scissor lift might be ideal. For outdoor construction sites with uneven ground, a diesel-powered rough terrain model with large tires and stabilizers would be more suitable. Always match your lift to the task to maximize both productivity and safety.
Conclusion: Making Smart and Safe Use of Scissor Lifts
Scissor lifts are a valuable asset across various industries, offering a practical solution for working at height. By understanding the types available, following safety protocols, and committing to regular maintenance, you can ensure your team stays productive and safe on every job.
Whether you’re managing a construction site, maintaining facilities, or stocking warehouse shelves, choosing the right lift and using it properly makes a significant difference. Take the time to train your team, inspect your equipment, and evaluate your specific needs before starting any elevated work. Safe operations begin with informed decisions.