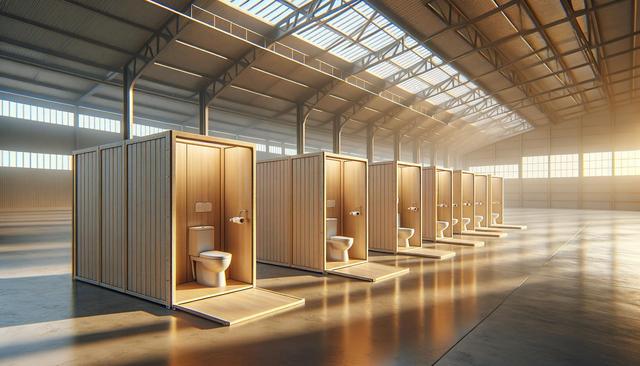
Streamline Your Build with Prefab Bathroom Pods: A Complete Guide
What Are Prefab Bathroom Pods?
Prefab bathroom pods are pre-manufactured, self-contained units that include all the essential components of a bathroom—plumbing, electrical systems, fixtures, and finishes—assembled in a controlled factory environment. Once complete, these units are delivered to construction sites ready for installation. This approach is increasingly popular in sectors such as hospitality, healthcare, student housing, and residential developments due to its efficiency and consistency.
The concept behind prefab bathroom pods is rooted in modular construction, where building elements are produced off-site and then assembled on-site. By removing the variability of traditional construction methods, builders can achieve more reliable timelines and consistent quality. These pods are designed to meet local building codes and can be customized to various design specifications, making them suitable for a wide range of projects.
Some key components typically included in a prefab bathroom pod are:
- Shower or bathtub unit
- Toilet and sink with appropriate plumbing
- Lighting and ventilation systems
- Wall and floor finishes
- Pre-wired electrical connections
This all-in-one nature reduces the need for multiple subcontractors, simplifies logistics, and enhances the overall coordination of the construction project.
Advantages of Using Prefabricated Bathroom Units
One of the primary reasons builders opt for prefab bathroom pods is the considerable time savings. Since the units are built off-site while the main structure is being constructed, on-site installation can be completed in just a few hours. This overlap of activities can shave weeks off the total project timeline.
Additional benefits of using prefab bathroom pods include:
- Improved Quality Control: Factory settings allow for more rigorous testing and consistent craftsmanship compared to on-site construction.
- Reduced Waste: Manufacturing in a controlled environment minimizes material waste and promotes sustainability.
- Labor Efficiency: Less reliance on skilled trades at the construction site can help manage labor shortages and reduce costs.
- Safety Benefits: Fewer workers on-site and less need for heavy tools or equipment reduce the risk of accidents.
These advantages make prefab pods especially valuable in large-scale developments where repeatability and consistency are key success factors.
Customization and Design Flexibility
Despite the standardized manufacturing process, prefab bathroom pods offer a surprising amount of design flexibility. Architects and designers can work with manufacturers to tailor units to specific project requirements, ensuring that aesthetics and functionality align with the overall vision of the build.
Customization options commonly available include:
- Choice of fixtures and finishes
- Layout and orientation based on room dimensions
- Accessibility features such as grab bars and walk-in showers
- Integration of smart technology for lighting and water usage
These options allow prefab pods to be used in both high-end developments and more utilitarian settings. The ability to replicate a customized design across multiple units also ensures design consistency throughout the building, which is particularly useful for hotels, dormitories, and apartment complexes.
Moreover, incorporating customized pods can simplify compliance with building codes and accessibility standards, as each unit can be inspected and certified before arriving on-site.
Installation Process and On-Site Integration
The installation of prefab bathroom pods is a streamlined process that requires minimal on-site preparation. Typically, the main structure must be ready to receive the units, which are then lifted into place and connected to plumbing, electrical, and ventilation systems.
Steps in the installation process often include:
- Delivery and placement of pods using cranes or forklifts
- Connection to existing building infrastructure
- Sealing and finishing work to integrate the pod with surrounding structures
- Final inspections and quality checks
Because the units arrive pre-tested and ready for use, this reduces the margin for on-site errors and shortens the commissioning phase of the project. Coordination among suppliers, contractors, and project managers is essential to ensure smooth integration and that all utility connections align properly with the building’s layout.
Proper planning during the design phase ensures that the infrastructure of the main building accounts for the pod dimensions and connection points—this foresight is key to avoiding costly delays or modifications during installation.
Applications in Various Sectors
Prefab bathroom pods are versatile and adaptable, making them suitable for a wide range of construction projects. In the hospitality industry, for instance, they are ideal for hotels where uniformity and quick turnaround times are essential. Healthcare facilities benefit from the hygienic and compliant nature of prefabricated modules, which can be designed to meet stringent medical standards.
Other sectors making use of prefab bathroom pods include:
- Student Housing: Rapid construction timelines support the academic calendar and reduce disruption.
- Residential Developments: Multi-unit buildings benefit from the efficiency and consistency of modular bathrooms.
- Senior Living Facilities: Accessibility and safety features can be built into each unit with precision.
- Workforce Housing: Cost-effective and durable solutions for temporary or permanent employee accommodations.
The scalability of prefab bathroom pods allows developers to maintain project timelines without sacrificing quality or design intent. Whether the goal is luxury or functionality, these units can be tailored to meet diverse needs across industries.