Understanding the Benefits of Durable and High-Quality Sandwich Panels
Discover more about durable and high-quality sandwich panels designed for superior insulation, strength, and energy efficiency. Ideal for industrial, commercial, and residential applications, these panels offer long-lasting performance, easy installation, and low maintenance for various building needs.
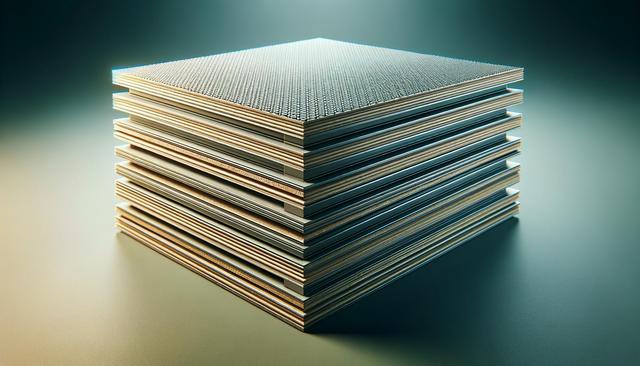
What Are Sandwich Panels and How Are They Constructed?
Sandwich panels are advanced construction materials composed of three layers: a core insulation material sandwiched between two outer metal sheets. This configuration offers an exceptional combination of structural integrity and thermal performance. The core is commonly made from materials like polyurethane (PUR), polyisocyanurate (PIR), mineral wool, or expanded polystyrene (EPS), each offering unique benefits in terms of insulation, fire resistance, and acoustic performance.
The outer layers, usually made from galvanized steel or aluminum, provide protection against environmental factors and mechanical stress. These panels are manufactured using precision processes that ensure strong adhesion between the layers, which is critical for durability and load-bearing capacity. This layered design enables sandwich panels to be lightweight yet strong, reducing structural load without compromising performance.
Applications for sandwich panels are widespread, with usage in roofs, walls, ceilings, cold storage facilities, and clean rooms. Their modular nature makes them a preferred choice in both new constructions and renovation projects.
Key Advantages of Using Sandwich Panels
Sandwich panels offer a wide range of benefits that make them a valuable building material across various sectors. Their popularity stems from their unique ability to combine durability, efficiency, and ease of installation in a single product.
Some notable advantages include:
- Thermal insulation: The core material provides excellent insulation, helping reduce energy consumption for heating and cooling.
- Fire resistance: Certain core options, such as mineral wool, offer high fire resistance, improving safety standards for buildings.
- Acoustic performance: Sandwich panels can also help reduce noise levels, which is beneficial in industrial and urban settings.
- Quick installation: Their modular design and lightweight nature simplify transportation and reduce labor time on site.
- Low maintenance: The robust outer layers resist corrosion, UV radiation, and mechanical damage, reducing the need for frequent repairs.
These benefits make sandwich panels a highly efficient and cost-effective solution for modern construction requirements.
Applications Across Industries
The versatility of sandwich panels makes them suitable for a wide array of industries and building types. They are commonly used in:
- Industrial buildings: Warehouses, factories, and production halls benefit from the panels’ thermal and structural properties.
- Commercial spaces: Shopping centers, office buildings, and showrooms use them for their aesthetic and functional qualities.
- Residential projects: Homes and apartments increasingly adopt sandwich panels for efficient and sustainable construction.
- Cold storage and clean rooms: Their superior insulation and hygiene-friendly surfaces are ideal for controlled environments.
In each of these applications, sandwich panels help reduce construction time and costs while enhancing the overall performance of the structure. Their adaptability ensures they can meet specific design and regulatory requirements for different sectors.
Environmental and Energy Efficiency Benefits
One of the standout features of high-quality sandwich panels is their contribution to energy efficiency and environmental sustainability. The insulation core significantly reduces heat transfer, minimizing the need for artificial heating and cooling. This leads to lower energy bills and aligns well with green building standards.
Additionally, many sandwich panels are manufactured using recyclable materials and processes that reduce environmental impact. Some manufacturers offer panels with certifications that verify their eco-friendliness, including compliance with energy codes and sustainable building practices.
Key environmental benefits include:
- Reduced carbon footprint: Lower energy usage translates into fewer greenhouse gas emissions.
- Recyclability: Most components, including metal sheets and insulation cores, can be recycled at the end of their lifecycle.
- Durability: Long lifespan reduces the need for frequent replacement, conserving resources over time.
These factors make sandwich panels a responsible choice for builders and developers aiming to create energy-efficient and environmentally conscious buildings.
Choosing the Right Sandwich Panel for Your Project
Selecting the most suitable sandwich panel depends on various factors, including the intended application, local climate, fire safety requirements, and budget. Understanding the properties of each core material is crucial:
- PUR and PIR: Offer excellent thermal insulation and are suitable for most climates.
- Mineral wool: Provides fire resistance and sound insulation, ideal for high-risk environments.
- EPS: Cost-effective and lightweight, best for less demanding insulation needs.
In addition to core material, consider the thickness of the panel, surface coating, and joint type, all of which influence performance. Consulting with a supplier or construction expert can help determine the right specification for your project.
It is also advisable to ensure that the panels meet local building codes and standards. Opting for certified and tested panels adds a layer of assurance regarding their performance and longevity.